It’s a question that surfaces frequently in the minds of retailers, designers, and curators: “Why are acrylic display screens so expensive?” On the surface, it appears basic. Acrylic is a type of plastic, and in a world saturated with affordable plastic products, a costs price can be perplexing. Nonetheless, corresponding a high-performance, optically pure acrylic display with an usual plastic container is like contrasting a precision-engineered Swiss watch to a non reusable toy. The products, the process, the skill, and the resulting efficiency are worlds apart.
The cost of a costs acrylic display screen is not approximate. It is a straight representation of an intricate ecosystem of aspects, consisting of advanced material scientific research, precision-heavy production processes, the high expense of skilled artisanal labor, and fundamental market economics. This essay will certainly deconstruct the price, moving past the surface to reveal the complex engineering and value proposal that justifies the investment. Understanding why it costs much more is the first step to valuing the enormous value a premium acrylic display screen brings to your brand name, your products, and your profits.
Table of Contents
It Starts at the Resource: The Inherent Cost of High Quality Acrylic
The trip of an acrylic display screen starts not in a workshop, yet in a chemical plant. The last cost is heavily influenced by the intrinsic cost and high quality of the raw material itself.
The Monomer Matters: From Raw Chemistry to Polymer Purity
The base element of all acrylic is a clear fluid monomer called Methyl Methacrylate (MIXED MARTIAL ARTS). Producing pure mixed martial arts is a complex, multi-stage chemical engineering process, even more engaged than the production of simple product plastics like polyethylene or polystyrene. The top quality and pureness of this monomer are extremely important; any impurities will certainly endanger the clarity, stamina, and lasting security of the final acrylic sheet. Firms like [ Mitsubishi Chemical Team ] (https://www.m-chemical.co.jp/en/products/departments/mcc/methacrylates/product/1200538_7599.html) are worldwide leaders in this customized field. This foundational price of producing high-purity MMA is the very first significant factor to the price of the final sheet.
The Story of Two Polymers: Cell Cast vs. Extruded
Once the mixed martial arts is created, it needs to be polymerized right into a strong sheet. There are 2 primary approaches, and the option between them represents the solitary most significant consider the material’s expense and quality.
- Extruded Polymer: This is the extra economical procedure. Molten acrylic polymer is required with a die and rollers to create a sheet. It’s faster and produces an extra constant thickness. However, the process conveys tension into the sheet, making it much less immune to chemicals and even more susceptible to melting or crazing throughout manufacture. It’s a good product, however not a premium one.
- Cell Cast Acrylic: This is the artisanal approach, booked for high-end applications. Fluid MMA monomer, along with initiators and additives, is poured in between 2 big panes of glass, which are then secured. This “cell” is after that slowly cured in heated water baths or autoclaves over numerous hours. This slow, stress-free process creates a harder, more robust, and a lot more chemically immune acrylic with exceptional optical clarity. It is the gold standard for top quality acrylic screens since it can be machined cleaner, brightened brighter, and solvent-welded more powerful. The labor-intensive, taxing nature of cell spreading makes it significantly extra expensive than squeezing out, however the performance benefits are non-negotiable for costs outcomes.
When you get a premium acrylic display screen, you are paying for the exceptional efficiency and workability of cell cast polymer.
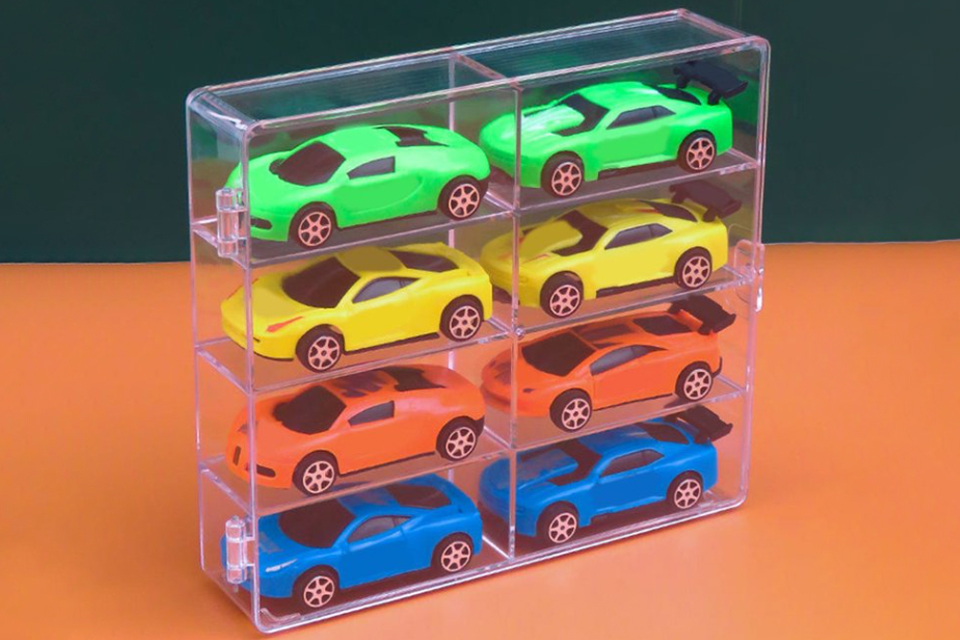
Integrated Luster: Ingredients and Special Formulas
Typical acrylic is currently excellent, however, for specialist display screen functions, it is frequently enhanced with performance-boosting ingredients. These are not totally free; they are specialized chemicals that add concrete value and cost.
- UV Stabilizers: To ensure the display screen remains clear for a years or even more without yellowing, and to secure the items inside from fading, unique UV-absorbing molecules are incorporated into the polymer matrix.
- Effect Modifiers: For applications calling for even greater strength, impact modifiers can be included in improve the product’s all-natural shatter resistance.
- Colorants: Achieving vibrant, regular colors calls for premium, light-fast pigments that are fully incorporated during the spreading procedure.
These enhancements turn a typical plastic sheet right into a high-performance design product, and this performance comes at a price.
Feature | Cell Cast Acrylic (Premium Displays) | Basic Glass | Economical Plastics (e.g., Styrene) |
---|---|---|---|
Product Cost | High | Modest | Reduced |
Optical Clarity | Excellent (92%) | Great (83-90%) | Poor (Commonly hazy or colored) |
Toughness | Excellent (High Effect & Shatter-Resistant) | Poor (Brittle, shatters alarmingly) | Poor (Brittle, cracks quickly) |
Construction | Excellent (Can be cut, curved, bonded) | Challenging (Requires specialized tools) | Restricted (Often injection built) |
Weight | Lightweight (50% lighter than glass) | Hefty | Extremely Light-weight |
Longevity/UV Stability | Exceptional (10+ years without yellowing) | Excellent (Does not yellow) | Poor (Yellows and becomes weak swiftly) |
Lifetime Worth | High (Acquire as soon as, lasts for years) | Modest (Danger of breakage/replacement) | Low (Requires regular substitute) |
The Art and Scientific Research of Manufacture: Where Ability Regulates a Premium
A sheet of expensive cast polymer is simply resources. Transforming it into a perfect, three-dimensional display box or stand is a labor-intensive procedure that needs costly machinery and, most importantly, very knowledgeable craftsmens. This is where a significant portion of the cost stays.
The Myth of “Simple Trimming”: Design a Perfect Side
Reducing acrylic for a premium display screen is not done with a handsaw. It requires accuracy equipment to produce edges that are flawlessly square, smooth, and dimensionally accurate to within a portion of a millimeter.
- CNC Routing: A [ Computer System Numerical Control (CNC) ] (https://www.autodesk.com/solutions/cnc-machining) router is an advanced device that can cost 10s or perhaps numerous countless dollars. It makes use of a computer-guided cutting device to perform an electronic layout with perfect precision. This makes sure every panel of a box is identical, a requirement for developing ideal, undetectable joints.
- Laser Cutting: A high-power CO2 laser makes use of an intense beam of light to evaporate the material, producing a tidy cut with a pre-polished side. These makers are additionally a significant capital expense.
Operating, programs, and preserving this equipment calls for skilled service technicians, whose competence is a vital price part.
The Unseen Seam: The Chemistry and Craft of Solvent Welding
This is perhaps the most misconstrued and skill-intensive part of creating a personalized acrylic screen . It is not “gluing.” It is a chemical procedure of fusing panels together.
- Preparation: The machined sides of the cast acrylic must be completely smooth and clean. Any imperfection will compromise the bond.
- The Weld: A watery-thin solvent is related to the joint. This solvent for a moment dissolves the surfaces, allowing the long polymer chains of the two panels to come together.
- The Blend: As the solvent evaporates, the entangled polymer chains solidify, developing a single, continual piece of acrylic.
A correctly implemented solvent weld is incredibly solid– often more powerful than the material itself– and perfectly clear. Achieving this bubble-free, unnoticeable seam requires enormous perseverance, a stable hand, and years of experience. This is not a production line job; it is a craft, and the time and ability of the producer are a key chauffeur of the final price.
The Final Polish: From Machined Side to Gem-Like Quality
The top edges of a display case or the sides of a strong block display need to be finished to recover optical quality. This is a multi-step, labor-intensive procedure:
- Sanding: The machined edge is thoroughly fined sand with gradually better grits of sandpaper to eliminate all device marks.
- Buffing: The sanded side is then polished on a high-speed buffing wheel making use of a collection of cutting and polishing compounds.
This process, which can take a significant quantity of time for a solitary piece, transforms a boring, opaque side right into one with dazzling, gem-like clearness. This level of finishing is a characteristic of a premium display screen and a significant labor price.
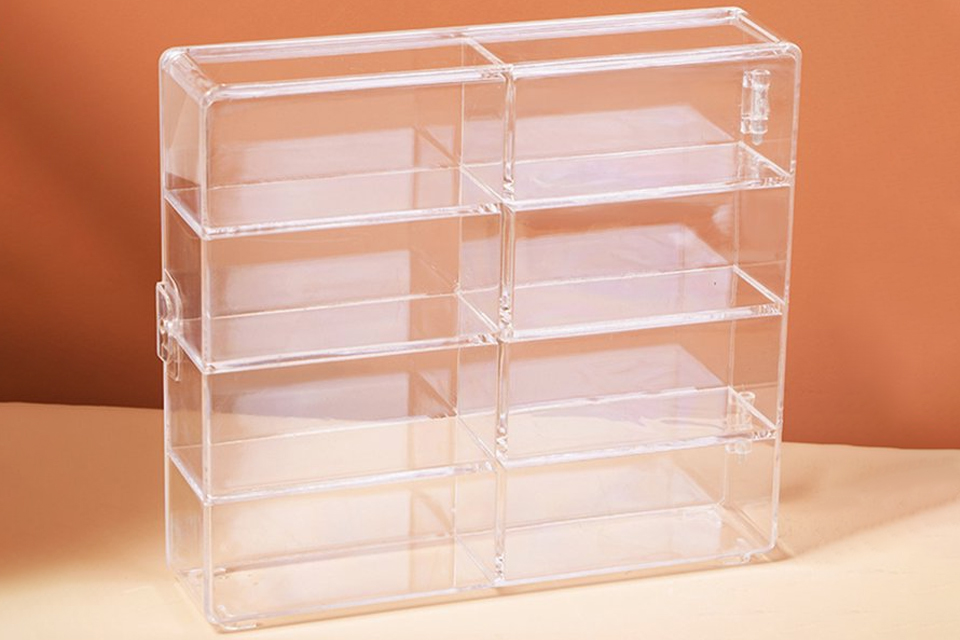
The Economics of Production: Unseen Expenses and Market Forces
Beyond materials and direct labor, numerous various other economic variables add to the cost of high-quality acrylic display screens .
The Causal Sequence: Supply Chain & Global Need
Polymer is not just made use of for display screens. It’s an essential material in style, automotive production, clinical devices, and signage. High demand from these large industries can stress the supply of the raw MMA monomer, driving up rates for every person. Additionally, as seen in the last few years, disruptions in the international supply chain– from resources lacks to logistical traffic jams– can trigger abrupt and substantial price walks. These market forces are outside the control of the maker however directly impact the last cost handed down to the customer.
The Human Aspect and Equipment Overhead
An expert construction store has considerable overhead expenses. This includes the home mortgage or lease on the center, the expense of the expensive machinery, recurring upkeep, and the high energy costs required to power CNC routers, lasers, and home heating ovens for thermoforming. Most notably, it includes the salaries and benefits of the competent craftspeople who are vital to creating a top quality product. Unlike a mass-produced product made by automated equipments, a customized acrylic display screen is heavily reliant on knowledgeable human labor, which is justifiably costly.
Cost Part | Approximate Percentage of Complete Price | Description |
---|---|---|
Basic Material (Cell Cast Acrylic) | 30% – 40% | The price of the state-of-the-art polymer sheet itself. Differs with thickness and type. |
Skilled Labor (Fabrication) | 25% – 35% | Time for CNC/laser configuration, cutting, flexing, and solvent welding by a skilled professional. |
Competent Labor (Completing) | 10% – 15% | The labor-intensive procedure of edge sanding, buffing, and polishing. |
Equipment Overhead & Energy | 10% – 15% | Amortization of expensive machinery, upkeep, and electrical power usage. |
Logistics & Service Overhead | 5% – 10% | Product packaging products, delivery prices, management, and revenue margin. |
- Note: These percents are illustrative and can differ dramatically based upon the intricacy, size, and quantity of the order. *.
Is It Worth It? The Concrete ROI of a Costs Acrylic Present.
Comprehending the costs is one thing; appreciating the value is another. A premium acrylic display screen is not an expenditure; it is an investment that offers a concrete return.
- The ROI of Assumption: A crystal-clear, faultlessly ended up screen raises the viewed value of the item inside. It interacts quality, expertise, and focus to detail– qualities that are moved to your brand name.
- The ROI of Toughness: A cheap styrene display could crack, yellow, and need substitute in less than a year. A well-crafted actors acrylic screen will last for over a years. The lower Overall Expense of Possession makes it the much more affordable option over time.
- The ROI of Protection: A strong, shatter-resistant acrylic case shields your valuable supply from dust, managing, and theft, serving as an insurance policy for your properties.
Frequently Asked Questions (Frequently Asked Questions).
Q1: Why not simply use glass? It’s often less expensive. . A: While the raw material cost of typical glass can be lower, glass is heavy (enhancing shipping expenses), exceptionally breakable (posing safety and security and breakage threats), and extremely hard and pricey to produce into personalized shapes. Acrylic’s mix of optical clarity, remarkable sturdiness, light weight, and construction adaptability makes it a far better general value for most display applications.
Q2: I found a much cheaper acrylic screen online. What’s the catch? . A: The “catch” is usually in the product and craftsmanship. Cheaper screens are normally made from slim, extruded acrylic which scratches easily and is fragile. The sides will be rough or inadequately brightened, and the joints will be made with easy glue, leaving visible, weak seams. It will look, feel, and carry out like a less expensive item.
Q3: Exactly how can I decrease the price of a personalized acrylic display screen? . A: The best means is to boost order quantity, as this permits the maker to maximize material use and labor. Simplifying the design, minimizing the variety of bends or complex cuts, and choosing a typical product thickness can also help reduce prices.
Q4: Does the density of the acrylic dramatically impact the rate? . A: Absolutely. The expense of an acrylic sheet is largely based on its volume. A 1/2″ thick sheet consists of two times the product as a 1/4″ sheet of the same dimension and will be about two times the price. The thickness also boosts reducing and brightening time, more contributing to the price.
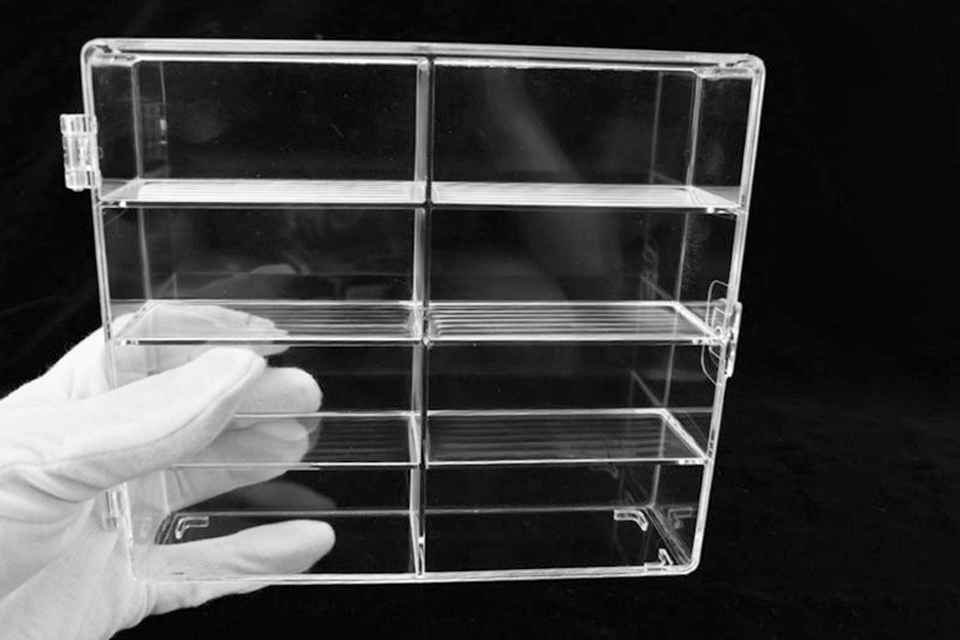
Verdict: The Rate of Value.
The cost of a premium acrylic screen is a straight and truthful reflection of what it takes to create it. It is the price of pure, engineered materials. It is the cost of advanced, accuracy equipment. And above all, it is the price of the irreplaceable time and ability of the craftsmens who transform a straightforward sheet into an object of transparent perfection.
When you purchase a costs acrylic display, you are not just buying a piece of plastic. You are getting an effective company tool– a tool that enhances your brand, safeguards your items, and delivers worth for several years ahead. Worldwide of aesthetic merchandising, you get what you spend for. And the rate of excellence is an investment that constantly pays dividends.