A box is rarely just a box. In the world of high-end retail, museum exhibition, or personal collecting, a container is a frame, a stage, and a guardian. It must present its contents with flawless clarity while simultaneously protecting them from the outside world. While off-the-shelf solutions exist, they often represent a compromise in size, quality, or function. For a perfect fit, a professional aesthetic, and uncompromising quality, the answer lies in engineering a custom acrylic box.
This is not a simple DIY project with a tube of glue. Creating a professional-grade custom acrylic box is an exercise in precision fabrication, material science, and meticulous finishing. It involves understanding the fundamental properties of acrylic, selecting the right materials and techniques for the job, and executing each step with engineering-level accuracy. The goal is to create an object where the seams are invisible, the angles are perfect, and the clarity is absolute—a transparent vessel that enhances, rather than distracts from, what is inside.
This definitive guide will walk you through the entire process, from initial concept to final polish. We will explore the science behind material selection, the physics of precision cutting, the chemistry of bonding, and the art of finishing. Whether you are a designer specifying a run of bespoke retail displays, a curator protecting a priceless artifact, or a dedicated maker aiming for professional results, this is your blueprint for engineering transparency.
Table of Contents
Phase 1: The Engineering Blueprint – Design & Planning
Before a single piece of acrylic is touched, the most critical work is done: the design and engineering phase. A flawed plan guarantees a flawed result. This stage is about defining purpose and translating that purpose into a precise, manufacturable design.
Defining Purpose and Performance Requirements
The first question is always: What is this box for? The answer dictates every subsequent decision.
- Retail Display: A custom acrylic box for a luxury handbag will have different requirements than one for small electronic components. It needs to be visually stunning, robust enough for a high-traffic environment, and perhaps incorporate features like locks or branding.
- Museum Vitrine: Here, the primary concerns are archival safety and protection. The box must be made from inert materials, offer UV protection to prevent fading, and be structurally sound to protect against accidents. The American Institute for Conservation (AIC) emphasizes such protective enclosures.
- Personal Collection: A box for a signed football or a collection of mineral specimens may prioritize clarity and a perfect fit, with less emphasis on the heavy-duty security of a retail fixture.
- Industrial/Lab Equipment Cover: In this case, function trumps form. The box needs to be dimensionally accurate to fit over machinery, durable, and perhaps resistant to specific chemicals.
The Science of Thickness: A Structural Decision
Choosing the acrylic sheet thickness is not just an aesthetic choice; it’s a structural engineering decision. The required thickness depends on the overall size of the box, the weight of the contents, and the intended use.
- 3/16″ (4.5mm): A good all-purpose thickness for small to medium-sized boxes (e.g., up to 12x12x12 inches) that won’t hold heavy items. It offers a solid feel without being overly bulky.
- 1/4″ (6mm): This is the industry standard for high-quality, medium to large-sized custom acrylic boxes. It provides excellent rigidity, a premium look and feel, and is suitable for most retail and display purposes.
- 3/8″ (9.5mm) to 1/2″ (12.7mm) and Thicker: Reserved for very large boxes, weight-bearing applications (like pedestals or tables), or when a “chunky,” high-end aesthetic is desired. These thicknesses are also used for specialized applications like aquariums or pressure-resistant enclosures.
Using a sheet that is too thin for a large box will result in bowing or flexing, which not only looks cheap but also puts immense stress on the bonded seams, risking eventual failure.
From Sketch to CAD: Ensuring Precision
While a hand sketch is great for initial ideas, professional fabrication relies on Computer-Aided Design (CAD). A CAD drawing translates the design into a precise digital file that specifies every dimension to the thousandth of an inch. This file can then be fed directly into CNC cutting machines, ensuring that all five or six sides of the box are cut with perfect accuracy. Without this level of precision, achieving the gap-free fit required for strong, invisible seams is nearly impossible.
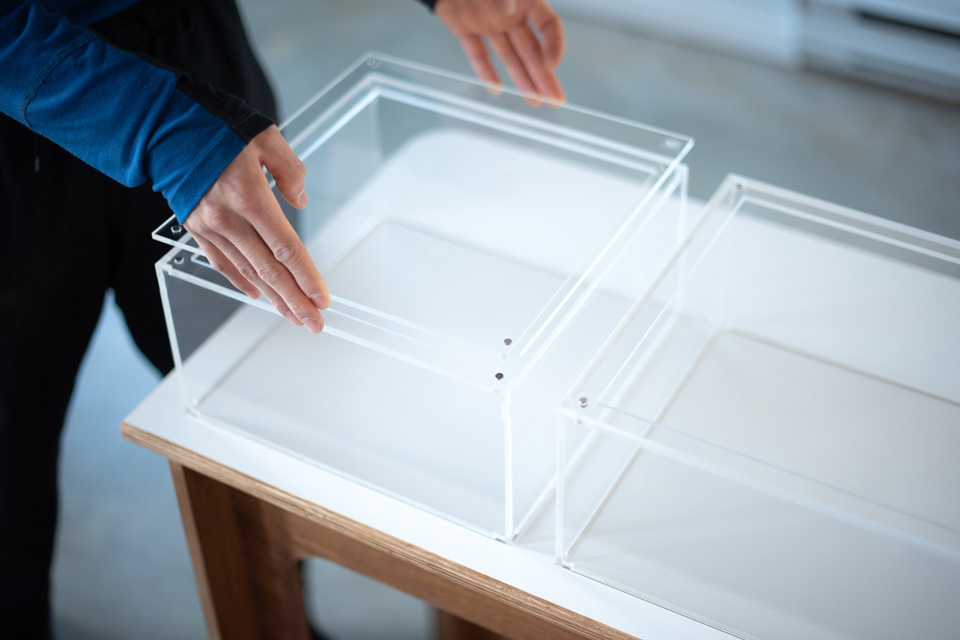
Phase 2: Material Mastery – Selection & Cutting
With a solid plan in place, the next phase involves selecting the right type of acrylic and cutting it with uncompromising precision.
The Fundamental Choice: Cast vs. Extruded Acrylic
Not all acrylic is created equal. There are two primary manufacturing methods—casting and extruding—and the choice has significant implications for a custom acrylic box.
- Extruded Acrylic: Made by pushing molten acrylic through a die, this is the more economical option. It has a lower melting point and is more prone to stress from fabrication. It’s suitable for simple projects, but its lower chemical resistance makes it a poor choice for high-strength solvent welding.
- Cast Acrylic: Made by pouring liquid monomer between two sheets of glass and curing it in a heated bath. This process produces a harder, more chemically resistant, and more optically clear sheet. It is the superior choice for high-quality custom acrylic boxes because it allows for stronger, cleaner solvent-welded seams and is easier to polish to a high gloss.
Feature | Cast Acrylic | Extruded Acrylic |
---|---|---|
Manufacturing Process | Monomer poured and cured in a mold | Molten polymer pushed through a die |
Chemical Resistance | Excellent (Ideal for solvent welding) | Good (More prone to crazing) |
Thickness Tolerance | Less consistent | More consistent |
Hardness/Scratch Resistance | Harder and more scratch-resistant | Softer and scratches more easily |
Laser Cutting/Engraving | Produces a clean, frosted engraving | Produces a clear, less distinct engraving |
Cost | Higher | Lower |
Best For | High-quality custom boxes, displays, polishing | General glazing, simple bent items, budget projects |
For any project where quality, clarity, and durability are paramount, cast acrylic is the unequivocal choice.
The Precision Cut: Creating Perfect Edges
The strength and beauty of a custom acrylic box are born at the edges. Each cut must be perfectly straight, smooth, and square.
- CNC Routing: The professional standard. A CNC router uses a digital CAD file to cut each panel with robotic precision. This method ensures all panels are identical and square, which is critical for assembly. The edge finish is a clean, machined matte that is perfect for bonding.
- Laser Cutting: For intricate designs or when a pre-polished edge is desired, a laser cutter is ideal. It cuts with a beam of light, vaporizing the material to create a clean, flame-polished edge. This is excellent for lids or decorative elements.
- Table Saw: For DIYers or simple straight cuts, a properly equipped table saw can work. The key is using the right blade: a high tooth-count (80-100T) blade with a Triple-Chip Grind (TCG) profile is essential to prevent chipping and cracking. The cut edge will be rough and require significant sanding and polishing before bonding.
Phase 3: The Moment of Truth – Assembly & Bonding
This is the most skill-intensive and critical phase. A slight misalignment or an improper bond will ruin the entire piece. The goal is to create seams that are not only structurally sound but also optically invisible.
The Foundation of a Flawless Seam: Edge Preparation
You cannot bond a rough or uneven edge. Before any bonding agent is applied, the cut edges (especially from a saw) must be prepared.
- Jointing/Sanding: The edge must be made perfectly flat and smooth. This can be done on a jointer (for a perfectly square edge) or by careful hand sanding on a flat surface, working through progressively finer grits of sandpaper.
- Cleaning: The edges and surrounding areas must be meticulously cleaned with isopropyl alcohol to remove any dust, oils, or residues that could interfere with the bond.
- Peel Back the Masking: The protective film on the acrylic sheets should be left on for as long as possible to prevent scratches. Just before bonding, carefully peel back the film about an inch from the edge to be joined.
The Science of the Seam: Solvent Welding
This is what separates professional custom acrylic boxes from amateur attempts. It is not gluing; it is a chemical fusion.
- The Chemistry: Thin, water-like solvents, such as those made by IPS Corporation (Weld-On), are used. These solvents work by temporarily dissolving the surface of the cast acrylic. When two such surfaces are pressed together, the polymer chains from each piece intermingle. The solvent quickly evaporates, and the chains become permanently entangled, fusing the two panels into a single, continuous piece of acrylic.
- The Technique (Capillary Action): The pieces are held together perfectly in a jig. A special applicator bottle with a fine needle tip is used to apply a small amount of the solvent to the inside seam. Capillary action—the tendency of a liquid to be drawn into a narrow space—pulls the solvent deep into the joint, filling it completely and creating a bubble-free, ultra-strong, and optically invisible bond. This requires a light, steady hand and a perfect, gap-free fit between the panels.
The Jig is Up: Ensuring Perfect Angles
Human hands cannot hold two panels at a perfect 90-degree angle with the consistent pressure needed for a solvent weld to cure. This is the job of a jig. A simple jig can be made from scrap wood or metal blocks clamped to a flat workbench to create a perfect right angle. The acrylic panels are placed in the jig, ensuring they are held securely and in perfect alignment while the solvent is applied and cures (which can take seconds for an initial bond, but up to 24-48 hours for full strength).
Phase 4: Beyond the Box – Finishing & Customization
A perfectly assembled box is a great achievement, but the work isn’t over. Finishing touches and custom features are what elevate a simple container into a bespoke product.
Lids, Hinges, and Functional Additions
A custom acrylic box can be much more than a five-sided cube. Common additions include:
- Lids: Shoebox-style lids, sliding lids, or lids with a simple finger-hole for easy lifting.
- Hinges: Acrylic or metal hinges can be added to create a functional door.
- Locks: Cam locks can be installed for security in retail or display environments.
- Bases: The box can be bonded to a thicker, colored acrylic base or a custom wood base for a more sophisticated look.
The Art of Personalization: Engraving and Printing
- Laser Engraving: A laser can be used to etch logos, text, or intricate designs onto the surface of the acrylic. This is perfect for branding, labeling, or adding a decorative touch.
- UV Direct Printing: Modern flatbed printers can print full-color, high-resolution graphics directly onto the acrylic surface. This allows for stunning visual effects and complete customization for marketing displays.
The Final Polish: Creating Gem-Like Edges
The top edges of an open-top box or the edges of a lid need to be finished to match the clarity of the acrylic face.
- Buffing: The most professional method. The edge is sanded smooth and then polished on a high-speed buffing wheel with special compounds. This produces a perfectly clear, flawless, gem-like edge.
- Flame Polishing: A faster method where a specialized torch is passed over the edge, melting the surface into a clear finish. While effective, it requires great skill and can induce stress in the material if done improperly.
Professional Fabrication vs. DIY: A Realistic Comparison
Should you hire a professional fabricator or try to build your own custom acrylic box? This table breaks down the realities of each approach.
Factor | Professional Fabrication | DIY Approach |
---|---|---|
Equipment | CNC Routers, Laser Cutters, Edge Finishers, Professional Jigs | Table Saw, Hand Tools, Basic Jigs |
Precision | Extremely High (to +/- 0.005″) | Variable; depends heavily on skill and tools |
Seam Quality | Optically Invisible, Bubble-Free Welds | Difficult to achieve; risk of bubbles, visible glue lines |
Material Cost | Access to wholesale pricing for cast acrylic | Higher retail prices for smaller quantities |
Total Cost | Higher initial outlay (labor + materials) | Lower material cost, but high “cost” in time and potential mistakes |
Time | Fast turnaround for single or multiple units | Very time-consuming, especially finishing steps |
Best For | Business needs, high-end displays, guaranteed quality | Hobby projects, prototypes, learning the craft |
Frequently Asked Questions (FAQs)
Q1: Can I make a custom acrylic box with super glue? A: No. Super glue (cyanoacrylate) is the wrong choice. It creates a weak, brittle bond and, more importantly, the fumes will cause “crazing”—a network of tiny cracks—to form on the acrylic surface, ruining its appearance. You must use a proper acrylic solvent cement.
Q2: What is the best way to clean my custom acrylic box? A: Use a soft, clean microfiber cloth with a bit of mild soap and lukewarm water. Gently wipe clean and dry with another clean microfiber cloth. Never use Windex or any cleaner with ammonia or alcohol, and avoid paper towels, as they are abrasive and will cause fine scratches.
Q3: How can I remove a scratch from my acrylic box? A: For light surface scratches, special acrylic polishing compounds (like Novus 2) can be used with a soft cloth to buff out the scratch. Deep scratches may require progressive wet sanding before polishing, a process best left to professionals.
Q4: Can my custom acrylic box be used outdoors? A: Yes, acrylic is naturally UV resistant and weather-proof, making it an excellent material for outdoor applications like signage or protective covers. Over many years, some yellowing can occur, but high-grade acrylics are very durable.
Q5: Are the bonded seams on a custom acrylic box waterproof? A: Yes. A properly executed solvent weld fuses the panels together, creating a seamless, waterproof joint. This is why acrylic is the material of choice for making custom aquariums and laboratory equipment.
Conclusion: The Pinnacle of Presentation and Protection
Creating a true custom acrylic box is a testament to the power of precision engineering. It is a process that transforms a simple industrial material into a sophisticated object of value. From the foundational decisions of the CAD blueprint to the meticulous chemistry of a solvent weld and the final, brilliant polish, every step is a deliberate move toward perfection.
While a DIY approach can be a rewarding challenge, for results that meet commercial, professional, or archival standards, partnering with a skilled fabrication specialist is essential. They possess the equipment, the expertise, and the experience to execute the design flawlessly. The result is more than just a box; it’s a crystal-clear, structurally sound, and perfectly proportioned frame that offers the ultimate in presentation and protection, allowing the object within to be seen and appreciated exactly as it was meant to be.